In this article we will answer how is nitrogen is produced for industrial chemical process? Nitrogen production from air.
Nitrogen is produced from dry air as we know by volume the air is composed of 78.09% nitrogen, 20.95% oxygen, 0.93% argon, 0.04% carbon dioxide, and small amounts of other gases.
Three types of unit or nitrogen plant can be used to obtain pure nitrogen:
- Membrane units “Membrane Nitrogen Generator”.
- Carbon Molecular sieve (CMS) units (Pressure-Swing Absorption (PSA)).
- Cryogenic separation.
Nitrogen Generation. | Capacity | Purity |
Membranes Separation. | 10-1000 m3/h | 90-99.5% N2 |
Pressure-Swing Absorption. | 10-5000 m3/h | 98-99.99% N2 |
Cryogenic Separation. | 100-7000 m3/h | <ppm O2 |
Nitrogen Membrane units
The nitrogen Membrane units used also to produce nitrogen production from air.
The compressed air, which has been filtered beforehand and from which oil has been removed, is sent through thousands of hollow fibres (membranes) consisting of a support and a fine layer of special polymer allowing different gases to be diffused through the membrane.
Certain gases possess a rapid diffusion speed (oxygen, water vapour, H2S), whilst others have a slow diffusion speed (nitrogen).
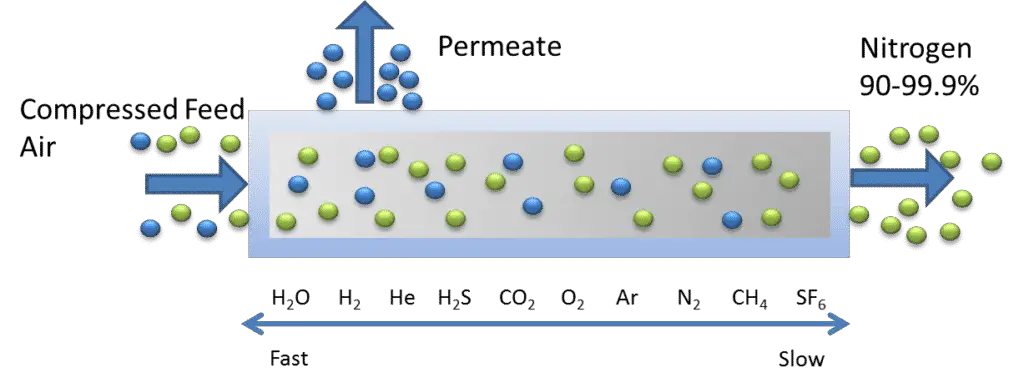
As it travels through the fibres, the air loses oxygen until it only contains nitrogen.
The longer the contact time, the purer the nitrogen will be, but the production costs will also be higher.
Since some of the nitrogen molecules are also diffused through the membrane, the system will consume more compressed air.
An oxygen analyser measures the purity of the nitrogen produced at the output point of a membrane string.
If the purity of the nitrogen decreases, an automatic system will increase the number of membranes in service.

A membrane unit consists of
- Air Intake particle filters.
- Air Compressor.
- Water Knockout Drum.
- Particle/ oil removing filters.
- Membranes.
- Trim Heater (to avoid condensation if the air is not dry).
- Nitrogen storage drums.
- Distribution network.
- Auxiliary equipment.
Oil removing filters,
The membranes are damaged by the presence of oil in the air or water on liquid phase.
Since the air compression is carried out by lubricated compressors, it is necessary to add a filtration stage upstream of the membranes.
Two 100 % oil removing active carbon filters are installed in parallel (1 in operation + 1 backup). The backup filter is isolated manually at the input and output points.
Particle filters,
As it passes through the active carbon filter, the air is liable to accumulate dust. Since these particles are noxious for the membranes, they need to be removed.
Two filters are installed in parallel (1 in operation + 1 backup) downstream of the oil
removing filters.
The head loss in each filter, oil remover and particle is measured and indicated locally.
Membranes,
The nitrogen production membranes (through the permeation of air) are installed in
parallel.
They are grouped together in one set of two membranes and one set of six.
Irrespective of the instrument air pressure between 7 and 10 bars at the input point of the unit, the membranes are supplied at a constant pressure thanks to the
expansion valves (1 in operation + 1 backup) situated upstream of the membranes.
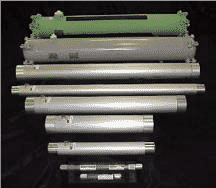
The nitrogen is produced at a constant pressure of around 5.5-7 bar abs.
The oxygen content of the nitrogen produced varies between 1 and 3 % depending on the production flow.
The flow of nitrogen produced is measured in Nm3/h at the output point of the unit whilst the O2 content is measured at the output point of the membranes.
Nitrogen storage drum,
The storage drum is situated downstream of the membranes and is supplied by their output manifold.
The low-pressure nitrogen distribution manifold is connected to the drum.
The drum is vertical and is protected against fire by a delivery valve which discharges in a secure zone.
Distribution network
The distribution network consists of sub-manifolds ¾” utility sockets are installed on each sub-manifold
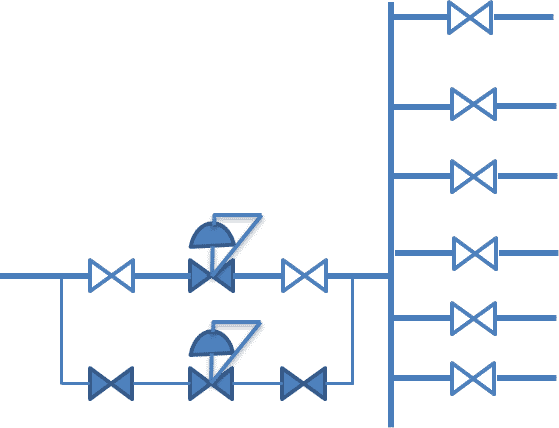
Nitrogen Molecular sieve units (Pressure Switch Absorber)
This process uses the adsorption technique with carbon molecular sieves to separate the compressed air into nitrogen and oxygen which lead to the nitrogen production from the air.
The theory of adsorption – the process by which molecules momentarily adhere to the surface of materials they are in contact with. The speeds at which the nitrogen and oxygen pass through the carbon micro pores are different; oxygen travels faster than nitrogen.
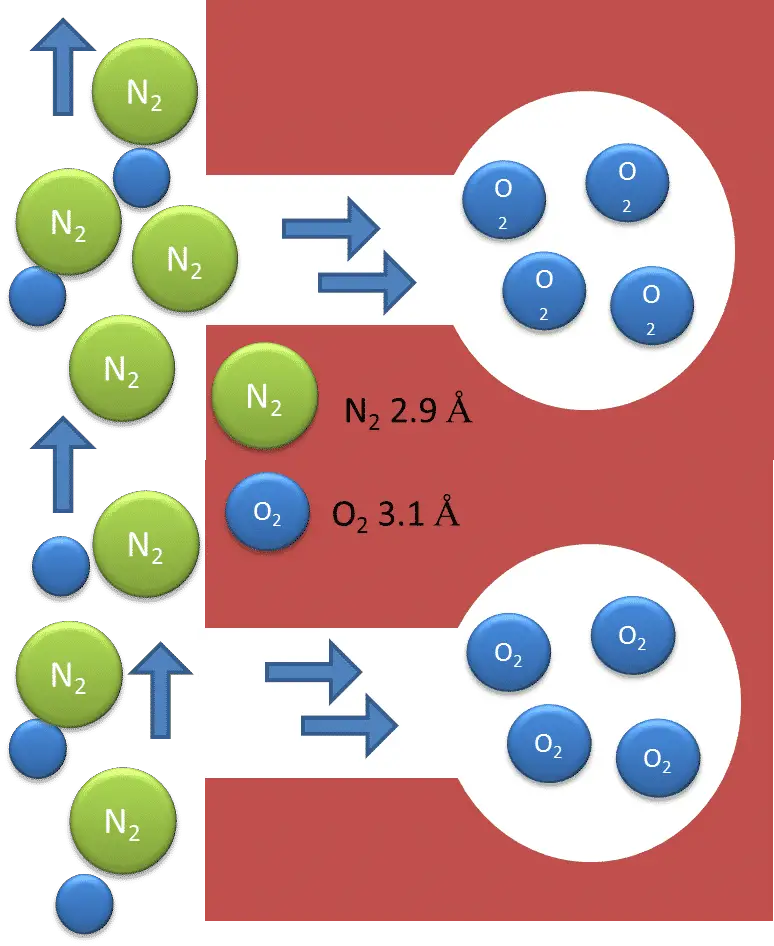
The process generally comprises 2 capacities; one for adsorption and the other for depressurisation.
The bed will be called saturated when oxygen molecules completely cover the surface of the pores and there is no more room available for adoption process to happen. The production units are generally supplied ready for use (skids) and are equipped with filters and automatic controls for commissioning and cycle lengths between adsorption and regeneration.
Nitrogen PSA Main Process Steps:
Adsorption N2 Generation
1. Pressurized air in.
2. Absorption of oxygen.
3. Generation of nitrogen out.
Desorption (depressursation) Regeneration
4. Equalization of pressure.
5. Regenerating bed depressurizes completely, allowing regeneration of the bed.
6. Waste gas through silencer.
PSA Detailed Process Steps:
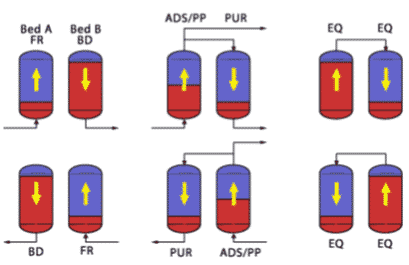
Bed A | FR | ADS/PP | EQ(down) | BD | PUR | EQ (up) |
Bed B | BD | PUR | EQ (up) | FR | ADS/PP | EQ (down) |
- FR= Feed Pressurization (pressurize to Adsorption pressure with FEED).
- ADS/PP= Adsorption and Provide purge (constant Pressure product gas and purge gas production).
- EQ(down)= Bed-to-Bed depressurization, bed on ADS/PP depressurizes top-top with bed completing PUR.
- BD= Blowdown or countercurrent depressurization of bed to vent/atmosphere in opposite direction of feed flow.
- PUR= Countercurrent purge of bed with product gas from bed on ADS/PP.
- EQ (UP)= Bed-to-bed re-pressurization with bed on ADS/PP, re-pressurizes top-top bed completing ADS/PP
Typical PSA Process Flow
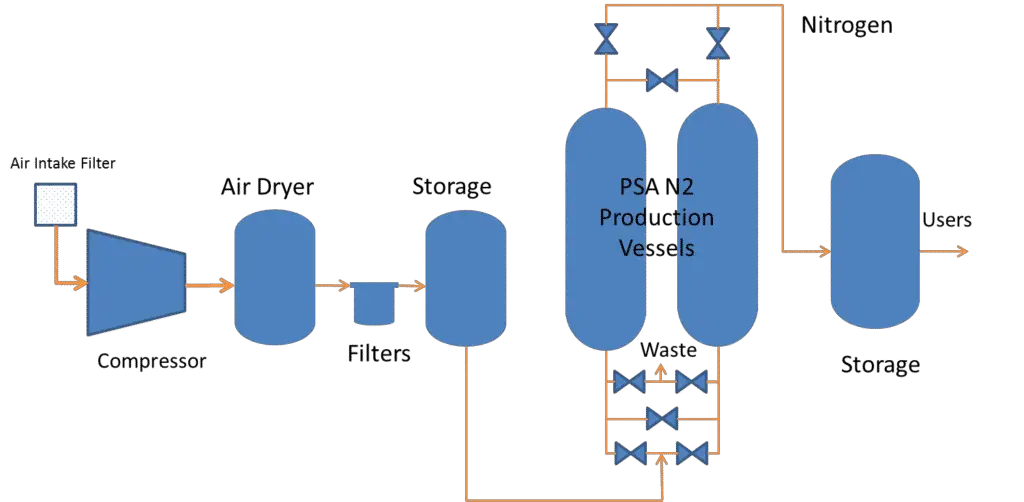
- Air intake filter and Compressor – Compressed air is required with all PSA nitrogen generators. The discharge pressure of the compressor is typically between 100-125 psig (6.9-8.6 barg), this air can be used to feed the PSA. Most of air compressors are equipped with air intake filter to avoid sand and particle.
- Air Dryer and Liquid separator –
The liquid separator is used to remove free water (condensate water) and oil from the compressed air. The PSA is very sensitive free water we should dry the air before send it to the PSA unit to avoid that it condensate inside the beds.
- Filters (coalescer filter, particle filter and activated carbon bed)– Used to reduce oil aerosols and oil vapour to make the air almost oil-free. For more details check the above sections regarding filter in the membrane unit.
- Process Air Receiver –
- PSA Nitrogen Generator
- Process Nitrogen Receiver
Cryogenic nitrogen plant
The cryogenic nitrogen plant is divided into three section:
- Warm end container : Basically in the section we is for compress the air (air compressor) and Clean (air purification unit).
- Cold box: this section is for separation of nitrogen, oxygen and water.
- Back-up system: finally this section is used only in case on failure of the of the cryogenic nitrogen unit.
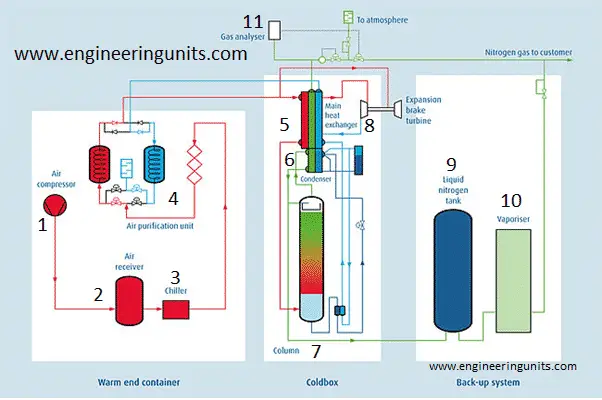
- Air compressor.
- Air receiver.
- Chiller.
- Air purification unit.
- Main Heat exchanger.
- Condenser.
- Column.
- Expender.
- Liquide nitrogen tank.
- Vaporiser.
- Gas analyser.
More to Read
- TOP 6 PRESSURE RELIEF CODES AND STANDARDS
- Different Types of Refrigerants
- Instrumentation Abbreviations Table – P&ID
- PSSR – Pre-Startup Safety Review
- TOP 6 PRESSURE RELIEF CODES AND STANDARDS
- Determine Compressibility factor, Z Factor
For more reading about Nitrogen Production – Cost Analysis – Nitrogen E11A